So, after the shutters were placed, the concrete poured and then left to harden, the next stage was removing those shutters.
It is crucial to leave the shutters on while the concrete goes off, or hardens. As stated before, concrete hardening is a chemical process, not a ‘drying out’ – the longer, within reason, you keep it wetted down, the harder it will become. Wetted down does not mean ‘keep it in liquid form, it means keep the hardening concrete damp this is aided , especially with columns, by wrapping those columns in plastic, once the formwork is removed.
This is not necessary with the ring beam – just remove (strike) the shutters once the concrete has hardened, and wash the beam down with water.
The team arrived bright and early to strike the shutters. K.Dee, the foreman had the team organised and everyone knew what to do.
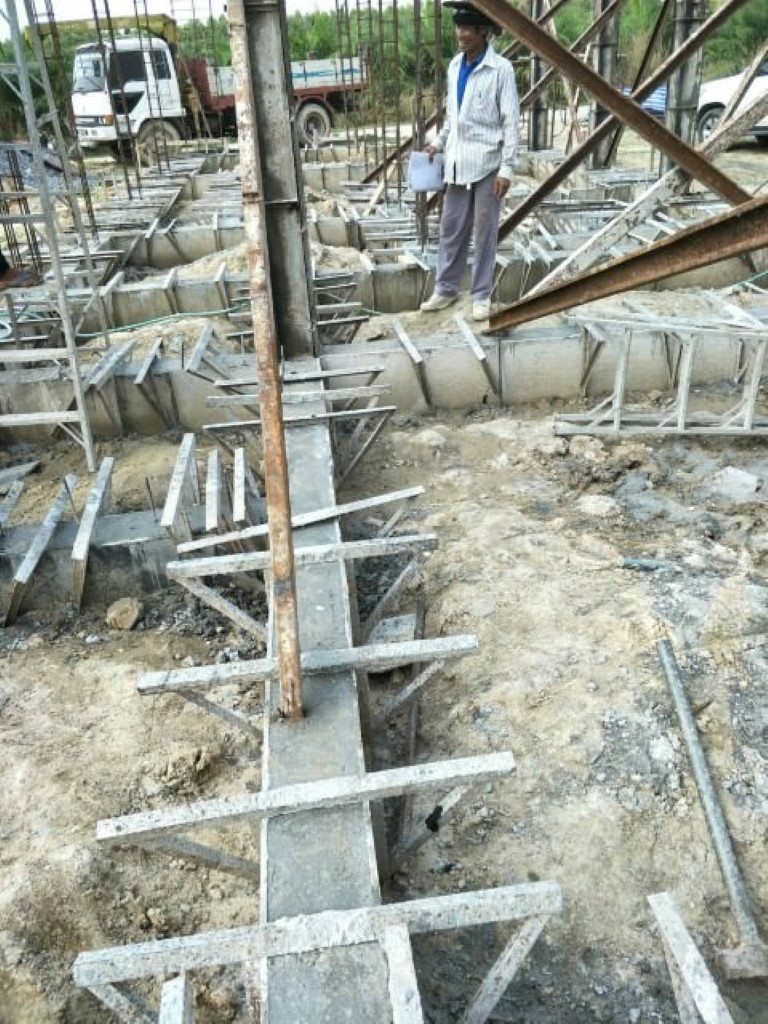
Firstly, a final check that it was ‘time’ to remove the shutters. Once completed, the next stage was the removal of the clamps holding the shuttering boards in place. Now, only the adhesion between the poured concrete, now in beam form, and the shuttering boards themselves were keeping those boards in place.
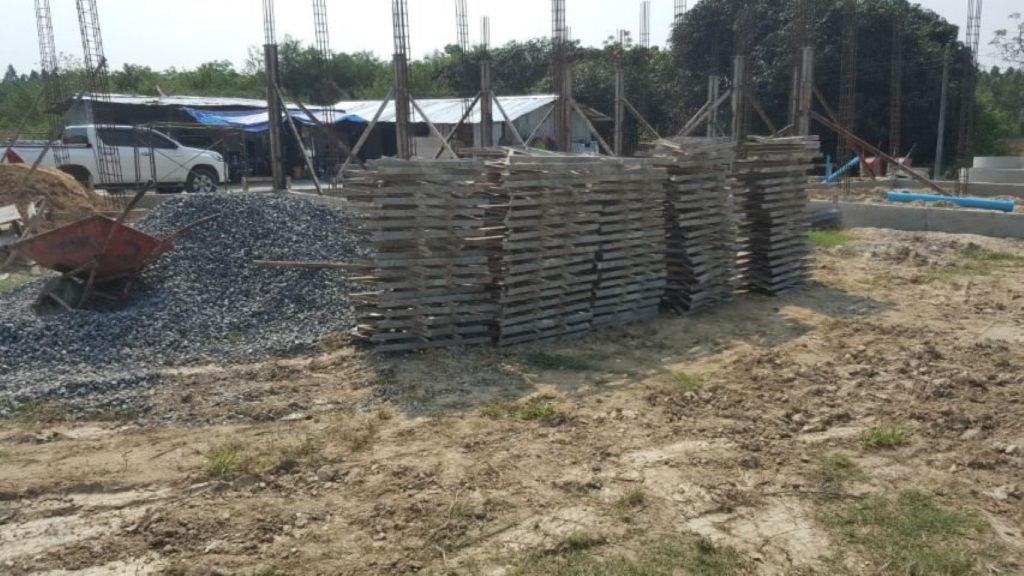
Before the concrete was poured, K.Dee had used a shutter release agent, a spray oil to make sure the shutters would come away cleanly. It is possible to apply the oil using a brush but it takes longer, and even using old engine or cooking oil – again, not the recommended option but some builders will use anything no matter how unsuitable , just to save a few dollars!
Now came the striking. It is said the word came from the action of hitting, or striking the top of the shutter (not the side) with a small hammer to break any residual bond from the treated shutter board. If it went to plan, the shutter board should just fall away, leaving a smooth surface on the cast concrete.
So it was with our ring beam. The team worked round the shutter boards, removing them. Some needed that tap with the hammer, some just fell away when the clamp were removed.
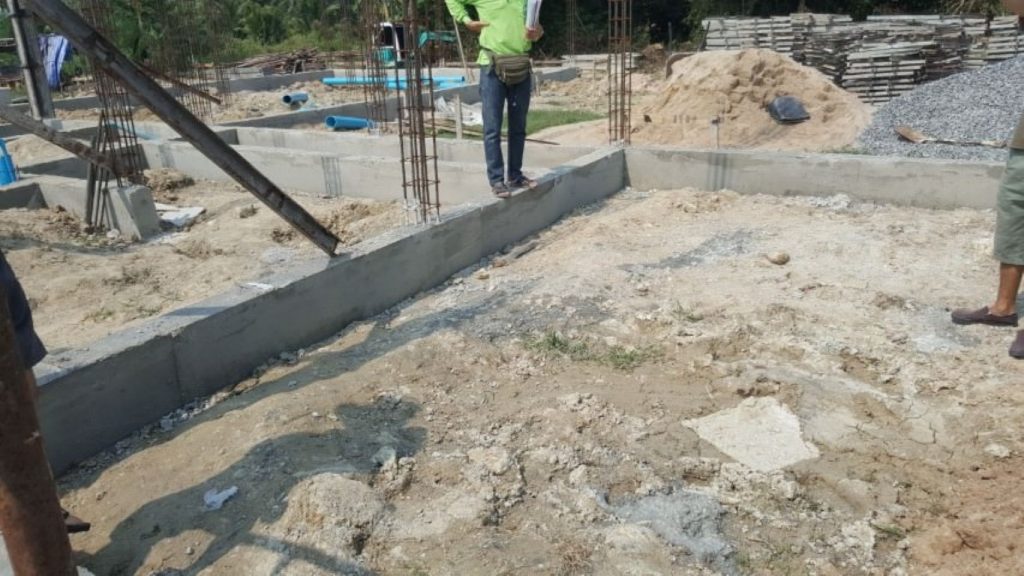
We ended up with a complex ring beam, and all ground floor cross-members making up the foundation design for the ground floor, and all sitting on the piles, that were described in an earlier post.
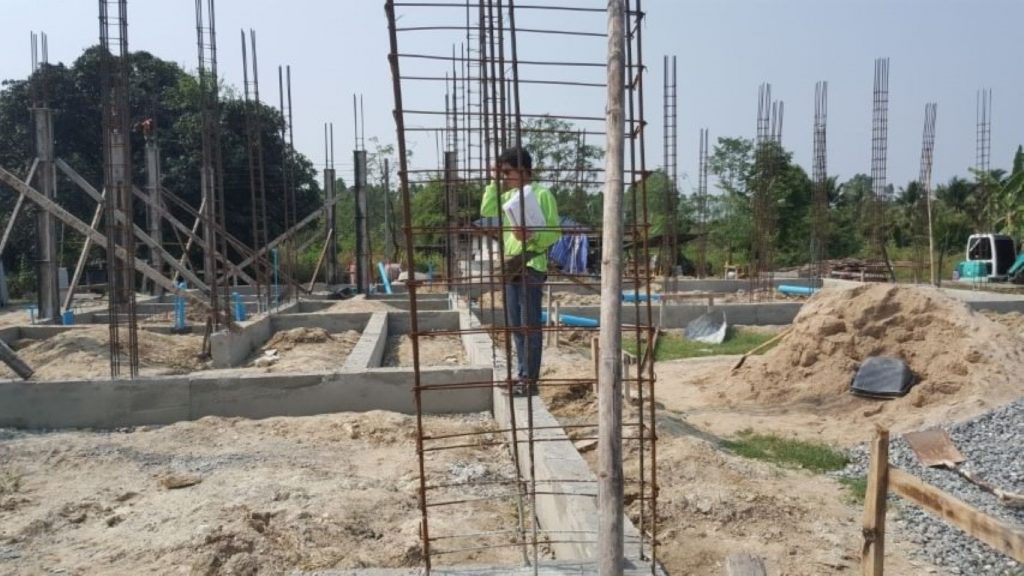
Growing out and up from this cast foundation were the rebar cages that were needed to form the ground floor uprights.., details for that are in an upcoming post in another post.