With the first-floor ring beam now cast, the next stage is the placing of the floor planks.
As before, K.Pot checked the ring beam was solid and ready, then re-checked the spans between the beams. This was to ensure the right length planks were purchased.
As mentioned before, it is not only the length calculation to specify the planks. As the length increases, it is important to make sure the plank can carry the load – longer planks require a greater density of rebar inside, and may even become thicker as a result of the increase in steel
With the required information gathered, he placed the order with the plank supplier. A few days later, the flatbed truck turned up, loaded with planks. The planks had been loaded in a systematic way so that they could be unloaded in a sequence of placing. This was also worked out by the builder beforehand, to make the plank placement a lot easier.
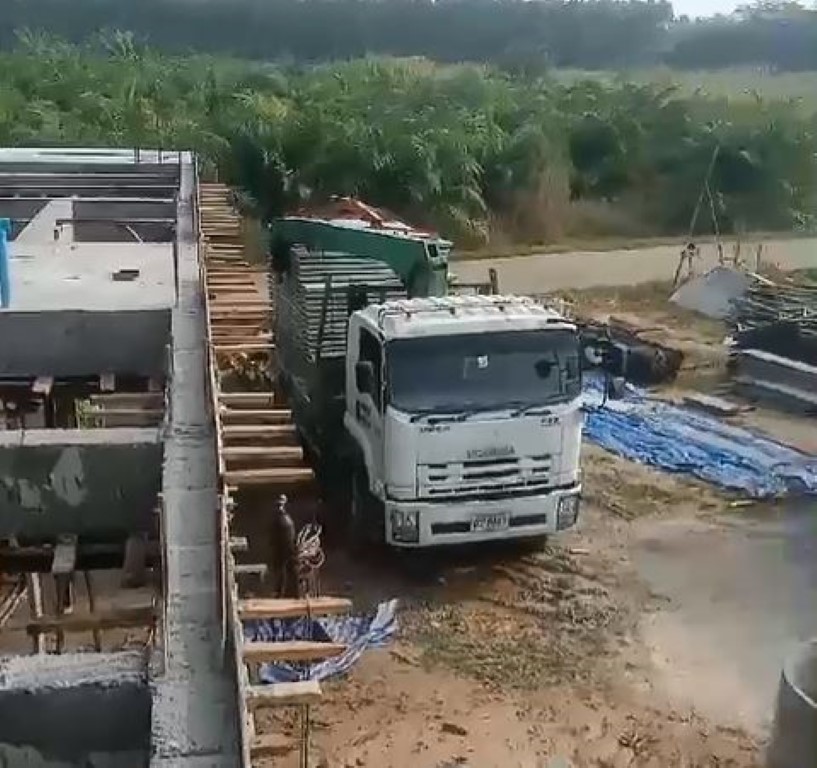
The truck came with a crane attachment and further, a lifting frame so that multiple planks could be raised up in one lift. This speeded up the whole placement process.
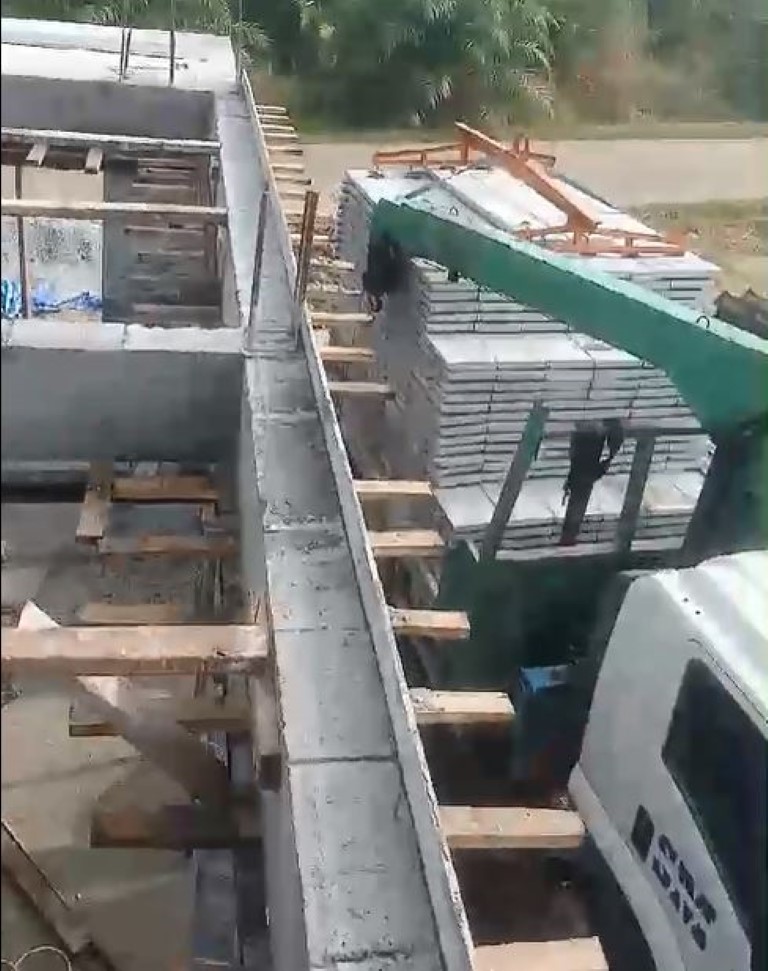
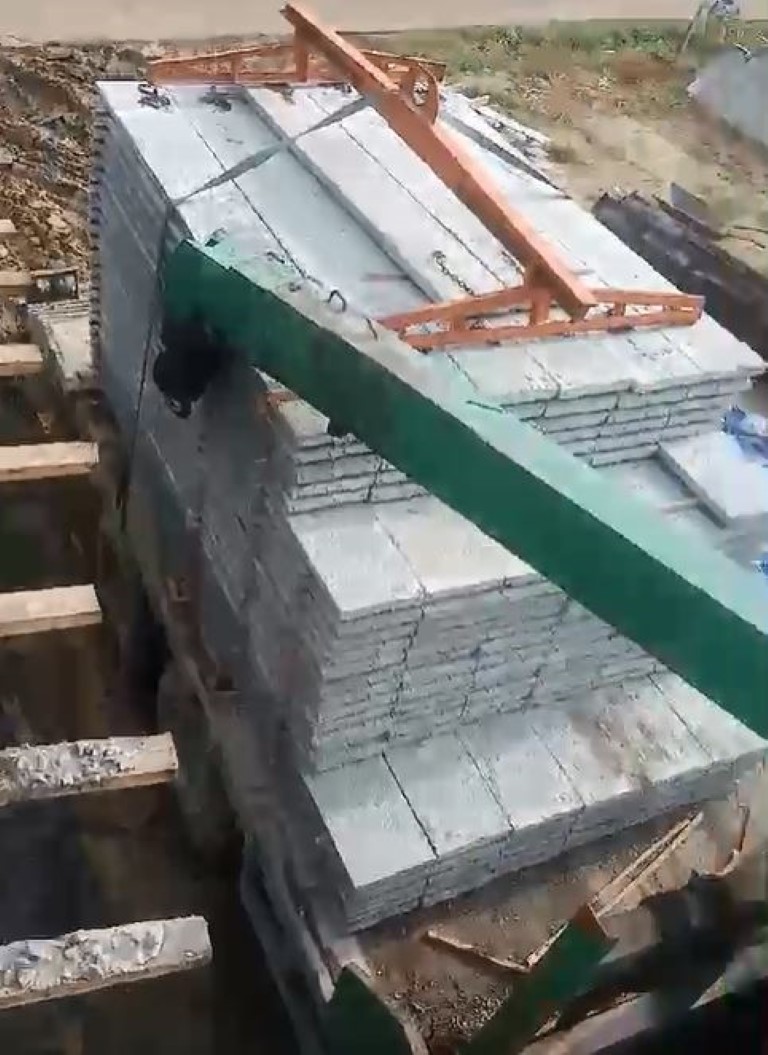
As each set of planks was raised, the building crew crow-bar’ed them into final position, making sure they were butted right up together. The first floor soon took on a solid appearance as the planks were placed, but it was important to remember… those planks were not yet secured, they were only sitting in position by the weight of the plank itself and could still move if any force was applied to them sideways and they could fall. With regards to this, while the plank placement was taking place, no one was allowed on the ground floor under the planks at all…safety first. The checking underneath came after all the planks were placed.
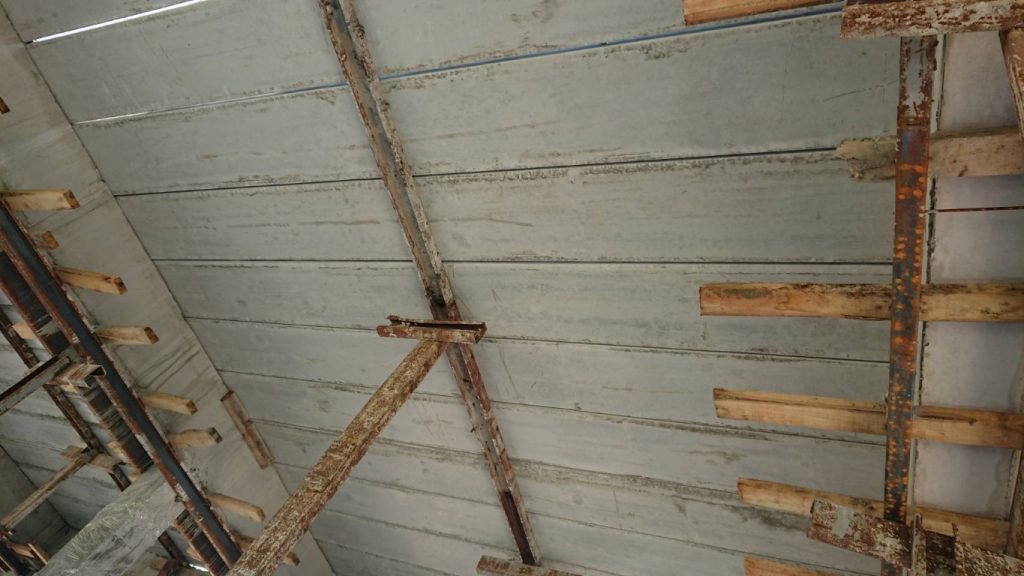
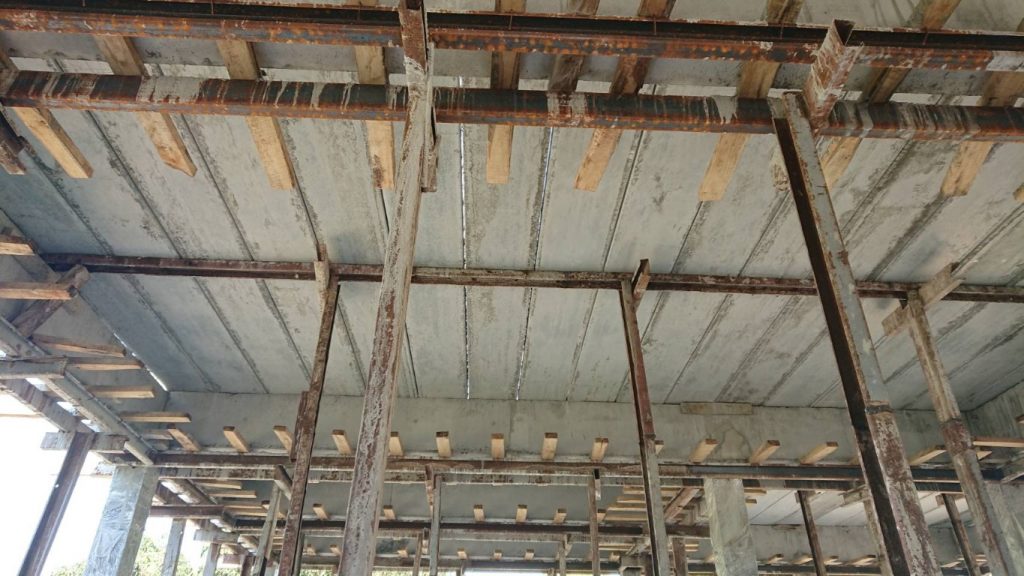
During the plank placement, it was necessary to make small cut-outs on some plank corners to fit around the locations of the first-floor columns
Finally, all planks were in place and the first floor was ready for the next stage – re-enforcing mesh placement and concreting, but before that, another separate stage had to be completed – the casting of the first floor columns.