One of the aims of this construction was to include traditional features in the build – roof style, overhang, window proportions and wood panelling detail. A particular and central feature of traditional Thai Lanna and Ayutthaya houses is the Sala.
The Sala was an important part of the traditional Thai house – it was the link between the house occupants and any visitors. Anyone arriving at the house would meet the householder ‘ halfway’ in the Sala. It was only after introductions and some initial conversations that the householder could decide whether or not to invite the visitor into the house proper.
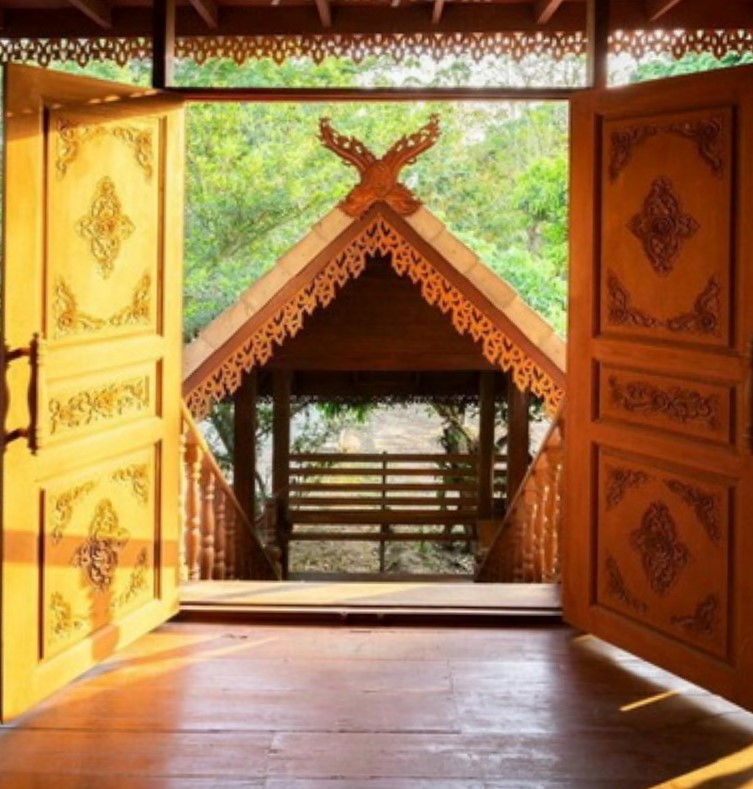
So, we wanted a Sala.
In traditional wooden Thai houses, the Sala would also be a wooden structure, but the Thai House Build was an RC-framed building. We wanted the strength of concrete but with the appearance of traditional wood, as much as possible.
The Sala in modern Thai buildings has in many cases become a ground-based family seating area in the same style as a gazebo. Other designs can have the Sala at the top of the stairs, actually on the same level as the main living buildings for the family.
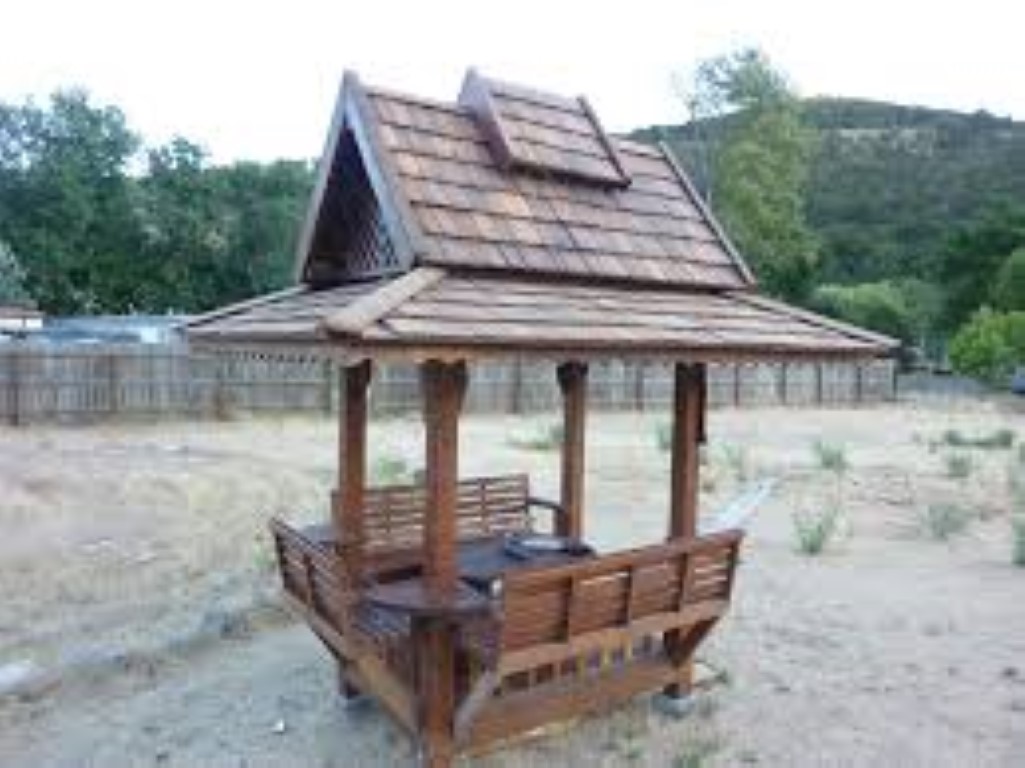
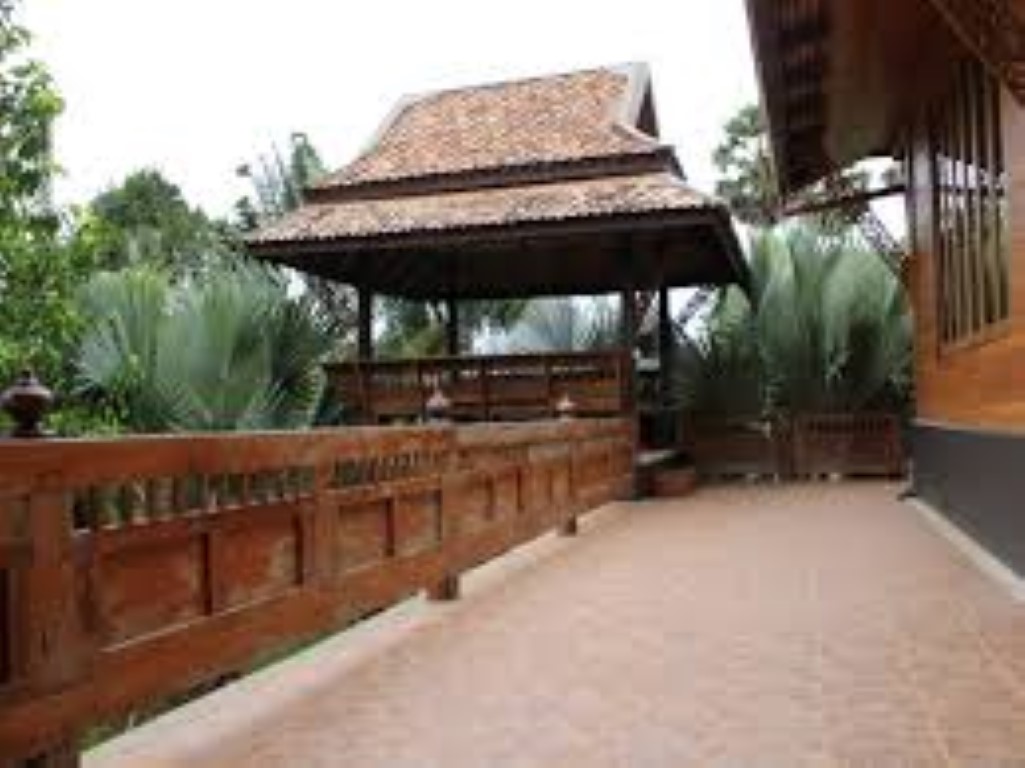
The Thai House Build Sala would be a two-staircase structure, with a seating/meeting area half way up. This roofed area had seating on two sides to provide the all-important meeting zone. The stairs would be tile-over-concrete but the bannisters would be wooden to create the wooden impression of the overall structure.

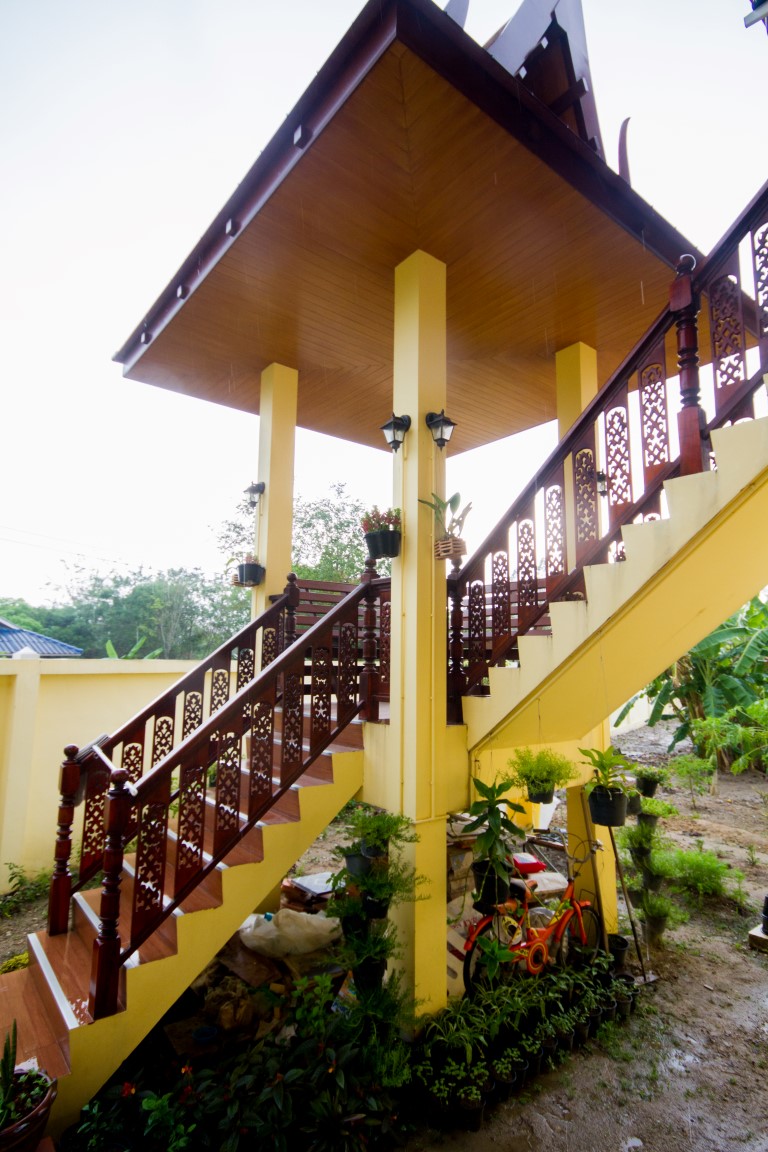
Location-wise, the Sala is usually situated at the front of the house, leading up to an open area from which all the house’s living rooms were located. We could not put the Sala at the front because we had a plan to put the swimming pool at the front, in an area we could ultimately close off for privacy. Therefore, our Sala was located at the back of the property, leading up from the area adjacent to the access point to the large outdoor covered area under Zone 2.
In traditional western-style houses, there is less need for such a structure – house owners simply come to the front door to greet visitors, as the living rooms are all on the same ground level. Traditional Thai houses though, have the living rooms on the first floor. This comes through history, when flooding could affect the ground floor of the house, and also animals might have been kept at the ground level.
Nowadays, that lower level of the house is often an open social area for the family, so the Sala might be rendered less important if meetings could take place in this area. However, we wanted to have the option, so the Sala was included in the design.