Around about this time, we needed to think about the plumbing lines – water in, and waste water out. In our build, this was further complicated by splitting the grey and black waste water, so that the septic tanks did not fill up every time we took showers or a bath!
Again… this is planning ahead. If the issue arises during the build, you are prepared for it. In this case, we had a plan in the future to use the grey water for irrigation. The septic tanks, all three of them, were for toilet waste only (see the separate post on tankage).
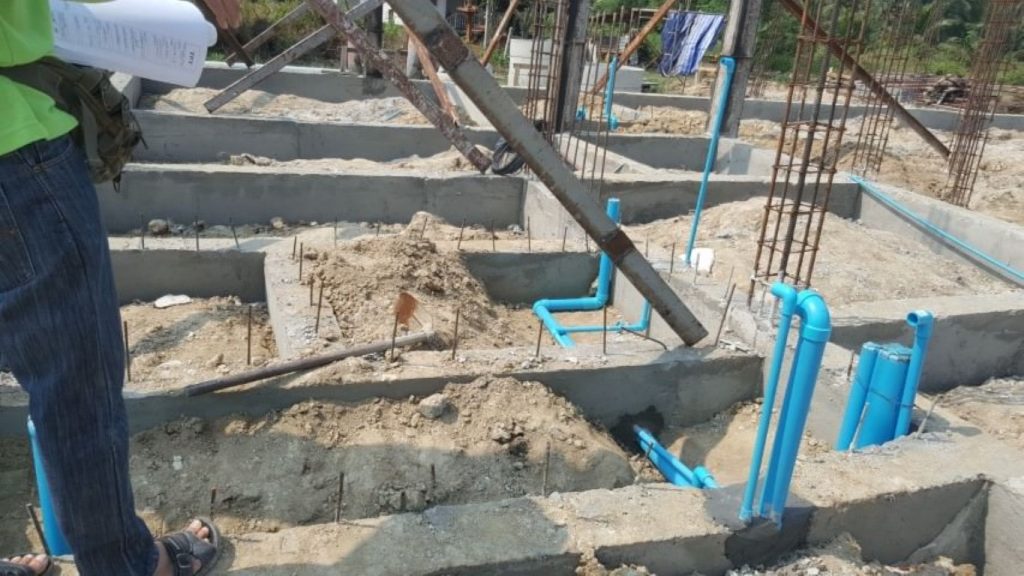
Our builder had experience in laying plumbing lines to get the correct slopes for efficient run off so no specialist was needed. As with most house builds, our actual build was 50cm above the surrounding, raised-up ground level. This made it a lot easier to get those ‘falls’. As it was detailed on the approved plans, we all knew the exact location of every shower, wash basin, sink, toilet and tap. Therefore, it was easy for the builder to mark that location on the ground, and lay the required pipework from each point to the external wall. This was of course carried out before the floor slab was cast.
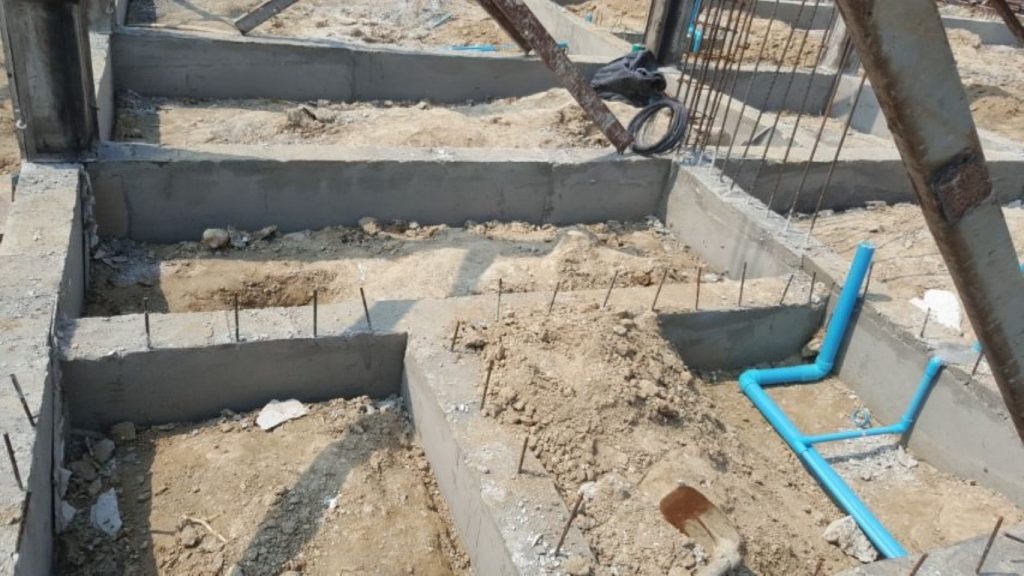
As part of the installation and where needed, the builder included the ‘P-traps’ in the line to prevent noxious odours coming back up the pipe and into the bathrooms. This another area that can be overlooked – make sure, if you are building in the future that this requirement is stated in the contract. You will have plenty of time, sitting in your new home and with a smelly drain, to regret for not planning this one!
In addition, we also fitted 40Litre grease traps to the outflow. This was necessary to ‘hold’ the oils / greases, etc. that were washed from plates and pans, from entering the grey water disposal area (field drain). If these traps were not fitted, the greases travelling down the line would congeal and ultimately block the drain field function. It’s an easier matter to periodically clear out those traps and they are much more manageable and accessible.
Termite control pipelines were also added at this time. In fact, as mentioned in our contract, I had forgotten to include termite control in the document! However, our builder was a professional. He knew it was a requirement and he had already built its inclusion into the costings. The pipe network and spray nozzles, terminating at various points around the base of the house, and all under the ground floor slab were placed, so when I came along, panicking at my omission, he had already laid those all-important termite lines under the ground floor slab!
The placement of all the plumbing and pest control concluded this part of the ground floor build. See the separate post on Termites elsewhere on this site.
Next we need to cast the ground floor slab.