Concreting
Yes! It’s concrete time, again…
With the steel and shuttering all in place and checked, K.Pot ordered the delivery of sufficient concrete to pour the entire ring beam in one go. It would have been too much to try and mix this quantity on-site, so mixer trucks were organised to deliver the wet concrete to the project.
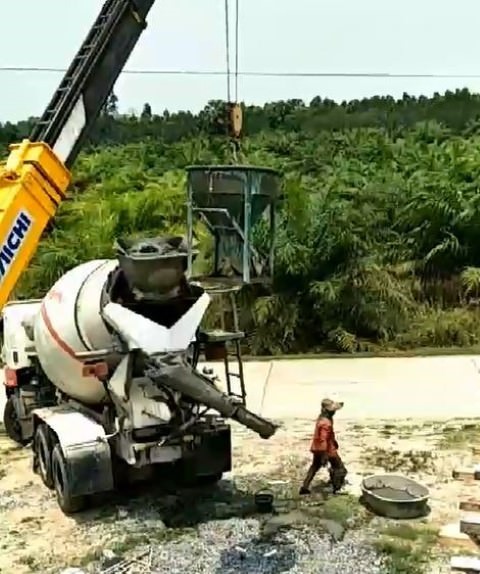
In the collection of work vehicles, the build team had access to a crane and concrete skip, so all the mixer truck had to do was reverse up onto the site and fill the skip. The crane would then lift the concrete batch up to the ring beam location, and the process was repeated until the mixer truck was empty.
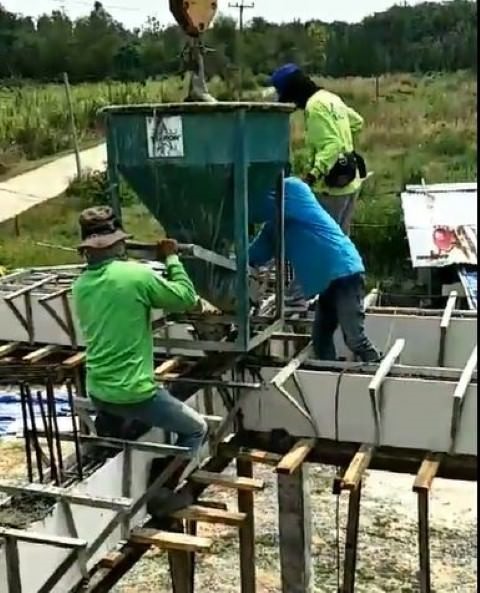
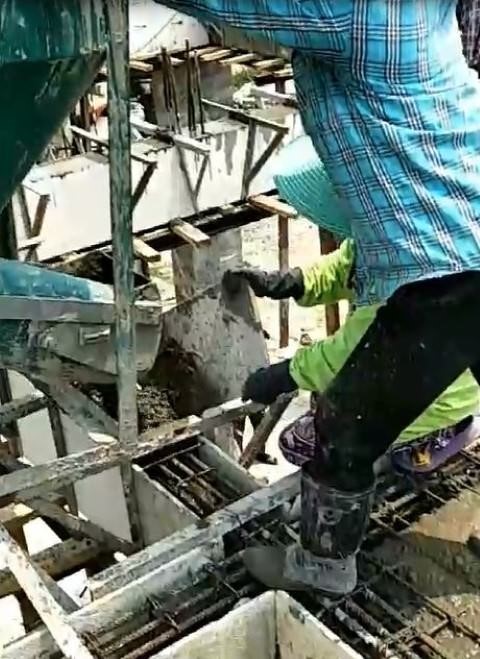
Once the trucks started arriving it was ‘all hands to the task’’ as the skip was repeatedly lifted to the ring beam, and unloaded into the shutter. Care had to be taken to make sure the shutter was totally full of concrete, but not over full and spilling out onto the floor below.
It was also important to make sure the concrete had ‘flowed’ around the steel rebar, so that there were no air-pockets inside the beam. Air pockets would create a weakness in the beam, which could lead to floor failure if the beam collapsed. To prevent this, the foreman allocated one worker to be in charge of the concrete vibrator to help the concrete completely enclose all the rebar.
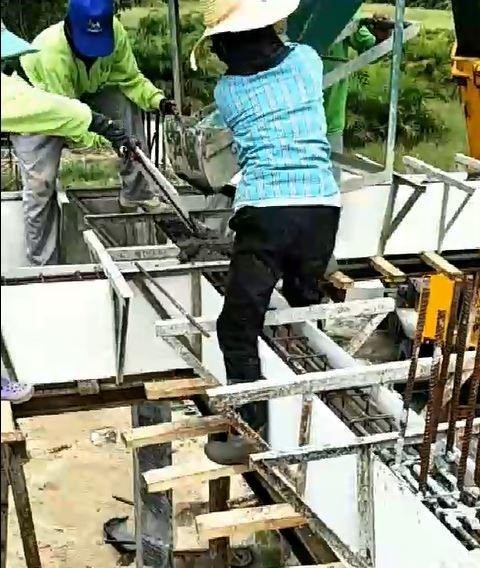
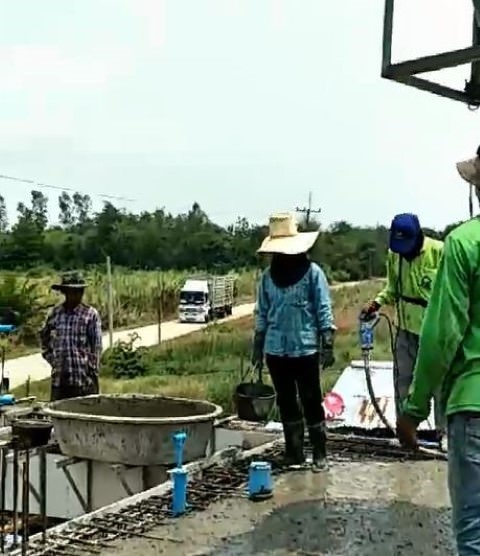
While the concrete pour was taking place, the foremen and one other worker were constantly checking the shuttering to look for leaks or possible failure potential. We think of concrete as a hard mass of rock-like substance, but in its wet-state it has hydraulic properties, especially with regards to pressure. Even in a shallow shutter, the mass of wet concrete is constantly pushing out, trying to escape the shutter, in a way that hardened concrete would not. The deeper the shutter the higher the pressure as you go down. It is less relevant in beam shuttering but much more so in column shuttering.
Once the bulk of the shutter pour had taken place, some finishing work on the shutter had to be carried out by hand. A smaller quantity of wet concrete was placed in a large bowl and then bucketed to where there was small dips in the surface, to bring it up to level.
At the same time as the beam was poured, the team also poured the floors for the bathrooms, which were lower than the actual beams, so that they were completed before the main floor slab (the next task) was planked and poured..
Terrіfic work! That is a great read.
Thanks for the story
thanks!